Rolling bearing precision components require corresponding caution when used. Not only does it change the use of high-performance linear bearings, but if they are not used properly, they cannot achieve the expected performance test results, so the following aspects of bearings are considered:
1. Keep the bearing and its surroundings clean. Even invisible dust bearing smiles will increase Timken bearing wear, vibration and noise.
2. When using installation, do not allow strong punching carefully, do not allow the use of hammer bearings, allow direct hit by rolling pressure.
3. Use appropriate and accurate installation tools, the use of special tools, try to avoid the use of fabrics and staple fibers.
4. To prevent the corrosion of NSK bearings, directly select the bearings by hand, fully wash the sweat on your hands, and apply high-quality mineral oil before starting, especially in the rainy season and summer, pay attention to rust.
After the bearing is installed in the host, there is a measurement index called cyclic rotation accuracy. This kind of change approximately repeats that the required number of revolutions represents the "quasi-period" of the cyclic rotation accuracy, and the magnitude of the magnitude change within the quasi-cycle is large, that is, the cyclic rotation accuracy is poor.
When proper preload is applied to the bearing spindle, this can gradually increase the speed to close to the working speed to implement the "run-in" effect of the linear bearing, which can improve the cycle rotation accuracy of the spindle.
There is a precision instrument that improves the accuracy of NSK bearings. When the main shaft uses 6202/P2 type bearings, but its accuracy still can not meet the requirements, then thicken the journal and make a raceway on it to replace the inner ring, and the steel ball is accurately measured, and the size is set every three pieces , Each group of steel balls is separated by an interval of close to 120°, due to the reduction of a heavy processing surface and a reduction of a matching surface, and at the same time, the rigidity of the shaft-bearing system is improved, and the maximum three balls are close to the minimum three balls The equidistant distribution also improves the rotation accuracy of the shaft, thus meeting the accuracy requirements of the instrument.
Click here for more details about NSK Bearing 20TAC47BSUC10PN7B.
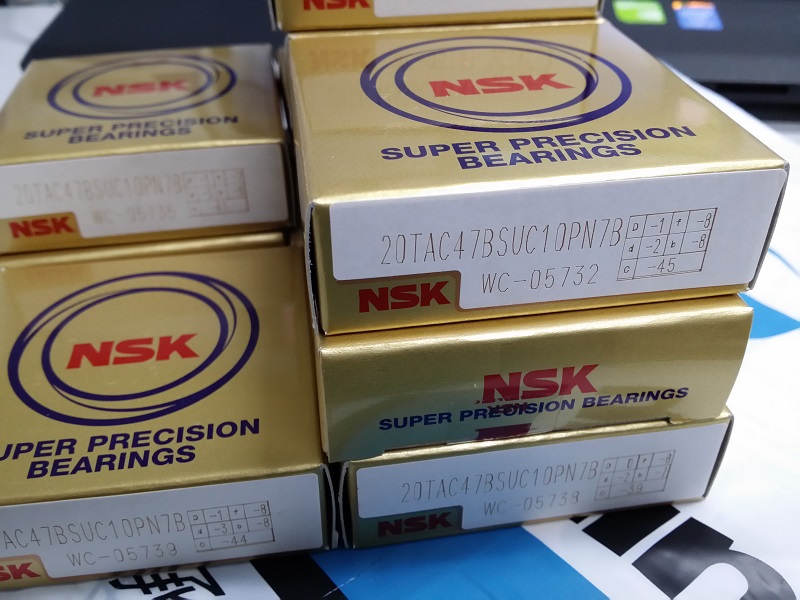
The comprehensive verification method of bearing installation accuracy is now specifically introduced. First, the linear bearing is installed into the main shaft of the bearing. The verification of installation accuracy goes through the following four steps:
1. Measure the size of the shaft and bearing housing holes to determine the accuracy of the bearing fit. The inner ring and the shaft adopt an interference fit, and the outer ring and the bearing seat hole adopt a clearance fit.
2. Installation of the fixed-end front bearing on the shaft: the bearing is thoroughly cleaned with clean kerosene, and then a certain amount of grease is filled into the bearing with an oil gun; the bearing is heated to increase the temperature by 20-30°C, and the NSK is used to Put the bearing into the shaft end; press the adapter sleeve on the shaft and press the bearing end surface with an appropriate pressure to axially position it; wrap the spring scale tape on the outer ring of the bearing and verify the provisions by measuring the starting torque Whether the preload of the company has changed significantly.
3. Install the bearing-shaft assembly into the seat hole: heat the seat hole to increase the temperature by 20 to 30°C, and install the bearing-shaft assembly into the seat hole with continuous gentle pressure; adjust the front cover to use the outer end surface of the bearing seat as For reference, put the dial head of the dial gauge against the surface of the journal, rotate the shaft to measure its runout, position the dial gauge on the shaft, and touch the inner surface of the rear seat hole, rotate the shaft to measure the front and rear seats of the bearing housing The coaxiality of the hole.
4. Put the free-end bearing selectively in the position that may offset the deviation, and install it in the bearing position behind the bearing seat to offset the roundness deviation and the coaxiality deviation as much as possible.